The experimental X-59 Quiet Supersonic Technology aircraft, or QueSST, built by Lockheed Martin’s Skunk Works for NASA, is really taking shape. The last time we had a good look at it, the plastic-wrapped plane was being transported on a semi-trailer en route to the company’s plant in Fort Worth, Texas, last December. Now that it’s there, the jet is no longer under wraps, and it has its nose fitted — quite probably the longest proboscis we’ve seen on an aircraft this size. The bizarre-looking snout is part of an overall design that’s tailored to reduce the kinds of sonic booms that have long been an obstacle in the way of commercial supersonic flight over land. Now at Fort Worth, the X-59 is being put through structural testing and is scheduled to make its maiden flight late this year.

The latest imagery of the X-59 in situ at Fort Worth was provided recently by NASA and shows the aircraft raised on jacks at the Texas facility where it’s undergoing its next phase of tests before returning to the West Coast. It includes a panoramic view that gives us the best look so far of that incredible nose. A nose so long that the pilot won’t even be able to see out in front of them, relying instead upon the eXternal Vision System (XVS) and an array of forward-facing high-resolution cameras. You can click here to see that panoramic shot in all its glory.
During its time in Texas, engineers are hoping to prove that the X-59’s structure is able to cope with the rigors of flight across the envelope. Fundamental to this is the supersonic regime, in which the jet is expected to replace the typical sonic boom with a ‘thump’ that NASA says “can barely be heard on the ground — if at all.” Another scientist from the agency described the effect as being “like distant rolling thunder or the slamming of a car door from a ways away”
“Our Texas site has existing facilities to perform the kinds of tests needed,” explained Lockheed Martin’s Mike Buonanno, an aerospace engineer and vehicle lead for the X-59. “In Fort Worth, they’ve got the perfect facility with a full control room and all the support equipment needed to do those tests very efficiently,” Buonanno said.
Some of that test equipment was left behind from the days of F-16 manufacture at Fort Worth before it shifted to Greenville, South Carolina. Not surprisingly, some changes needed to be made to the rigs to handle the X-59’s nose.
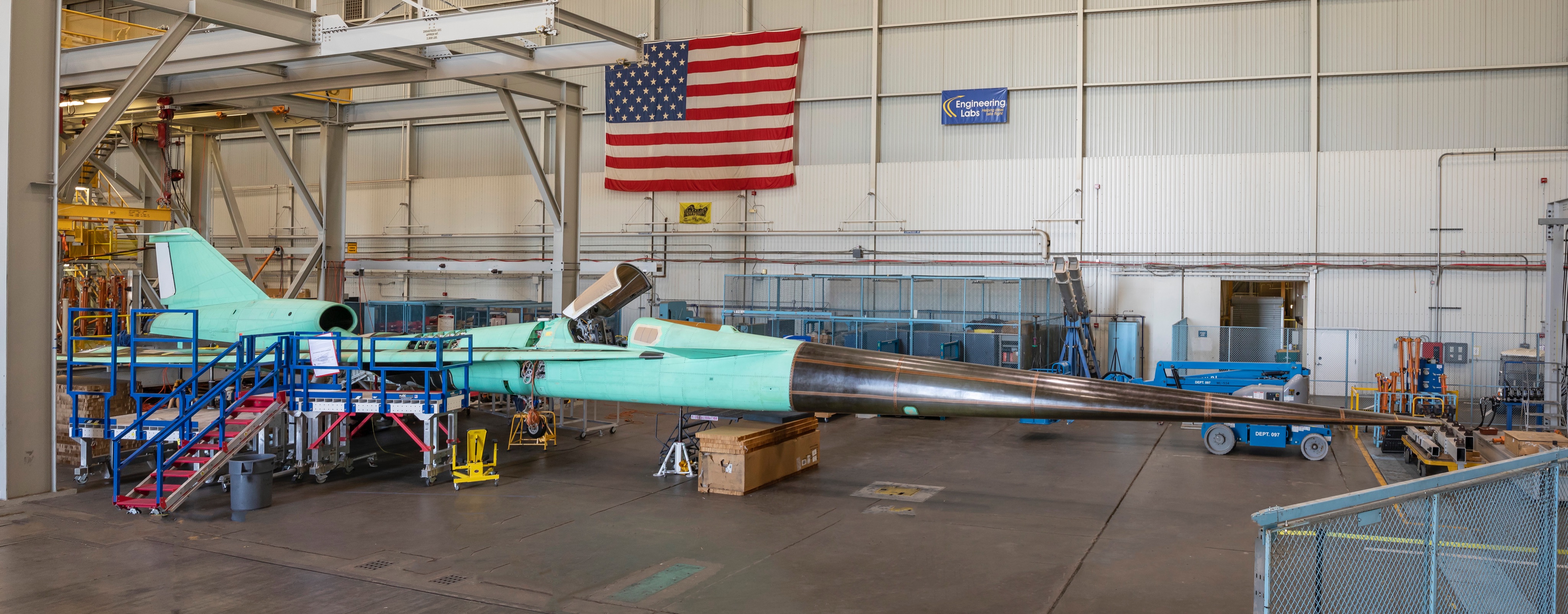
There are three specific areas of structural study being addressed while the X-59 is in Fort Worth, a site now best known for hosting the F-35 Joint Strike Fighter assembly line.
The first of these test areas is to ensure the jet can handle the anticipated loads during flight, including flying through turbulence, rapid turns, or landing. Any maneuver that might place pressure on the airframe is being simulated using mechanical arms that replicate the stresses, increasing them by 25 percent compared to what’s actually expected during flight.
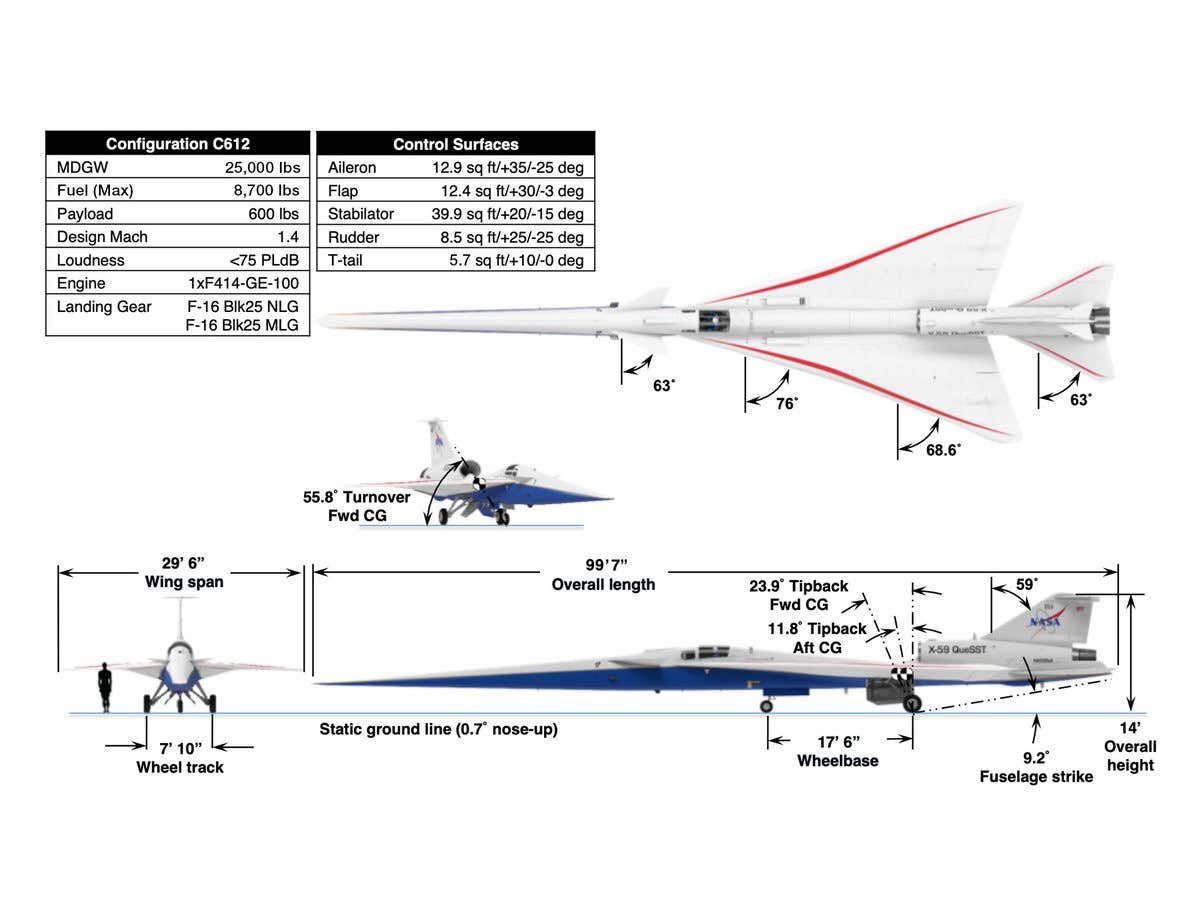
Second, sensors that are built into the X-59 are being tested to ensure they provide the pilot with an idea of the kinds of stresses being applied during flight. That’s basically a case of calibrating those sensors compared to the stress levels applied during the test.
Third, all the data collected is being compared with previous computer models to ensure that the structure behaves as expected.
All of this is especially important considering the X-59 is something of a Franken-plane, using components from a range of other designs. “Landing gear from an Air Force F-16 fighter, a cockpit canopy from a NASA T-38 trainer, a propulsion system part from a U-2 spy plane, and a control stick from an F-117 stealth fighter,” according to NASA.
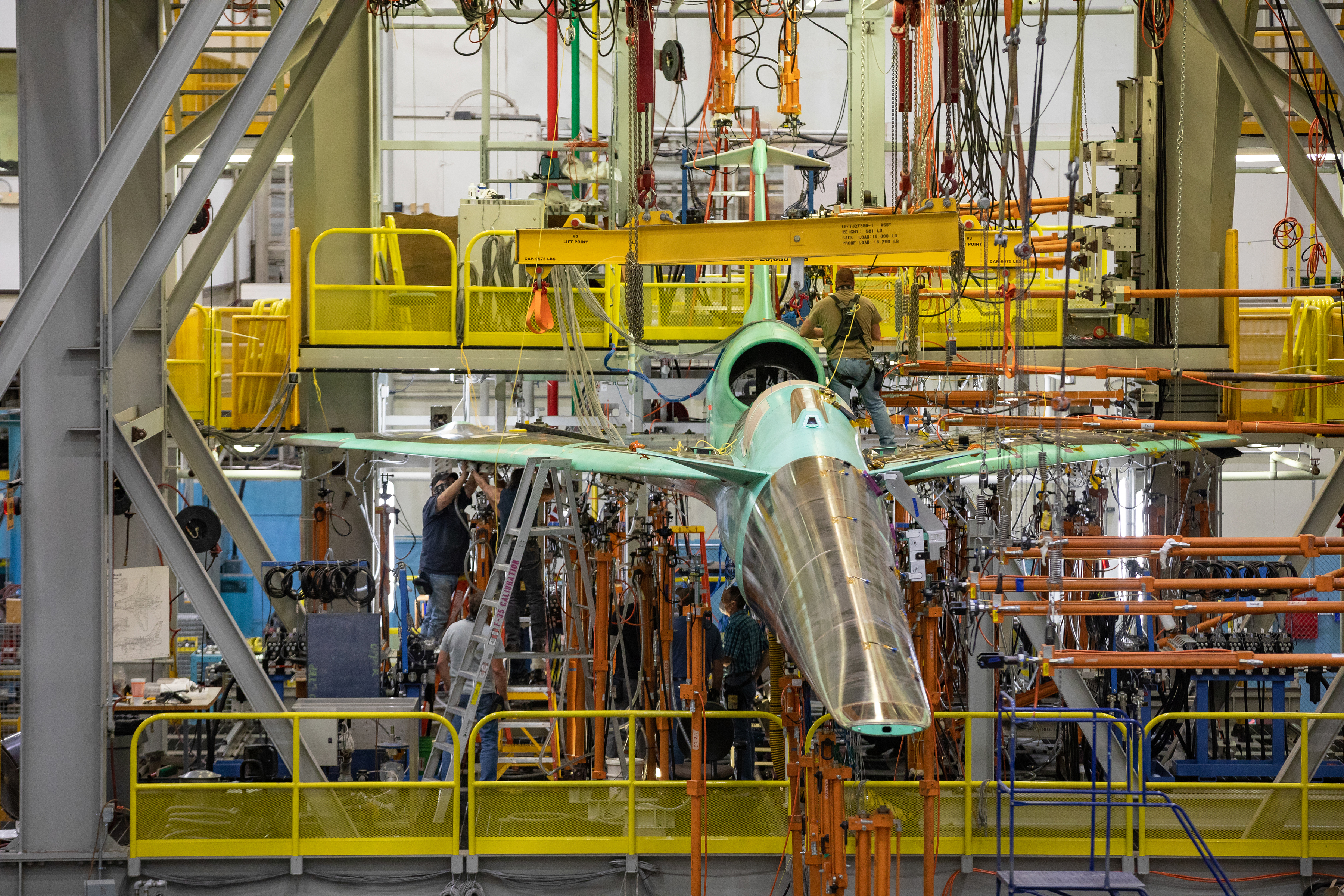
As of the last week of January around 80 percent of the structural tests had been successfully completed, NASA said.
Once those final structural tests are complete, the next thing to do will be to calibrate the aircraft’s fuel tanks, checking that the sensors that tell the pilot how much gas is left function at all attitudes.
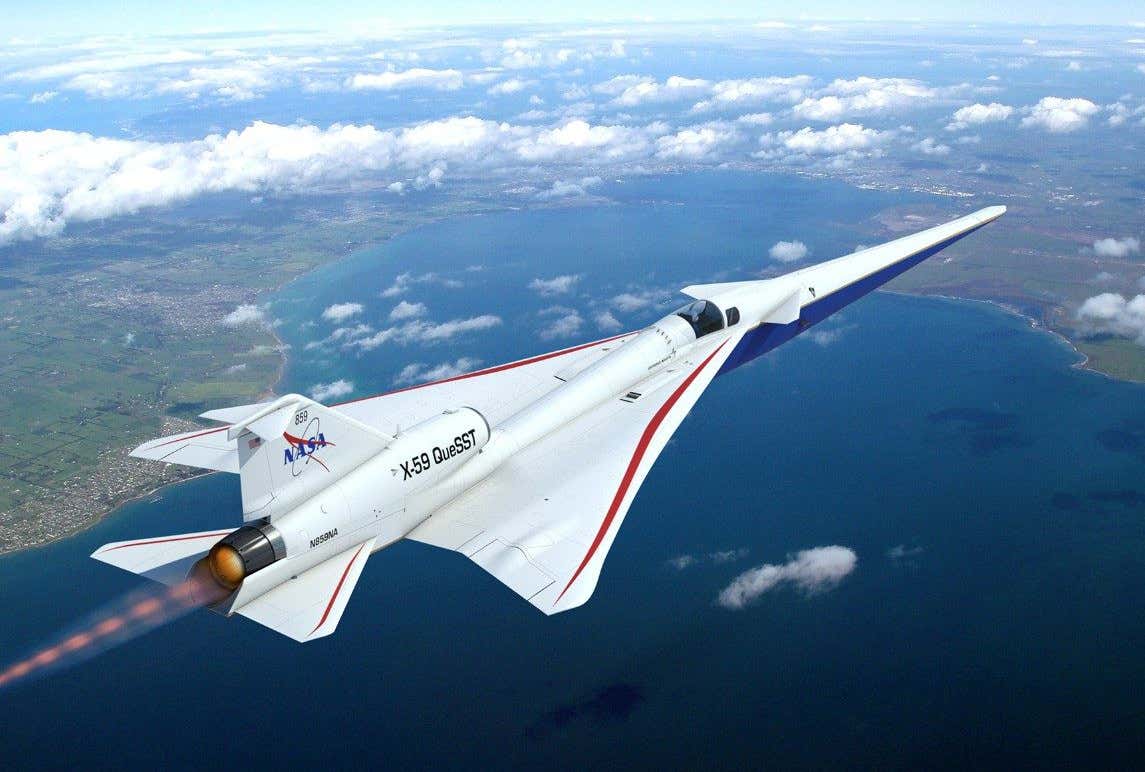
Then it will be time to return the X-59 to Palmdale, although there’s no precise timeline for this: “We will be in Fort Worth as long as we need to be there until we think the data is good, and everything has been performed to everyone’s satisfaction,” said Walter Silva, a senior research scientist at NASA’s Langley Research Center in Virginia.
At Palmdale, the X-59 will receive its modified General Electric F414 engine, landing gear, cockpit displays, and other essentials, making it ready for the flight test program to begin before year-end. The all-important noise testing is then expected to begin in 2023, followed in 2024 by a planned series of flights that will explore how communities actually respond to the aircraft’s sound when it passes overhead.
As we have explored in the past, there is an awful lot resting on the X-59. Should it perform as intended, demonstrating quiet high-speed flight, it could usher in a new generation of supersonic passenger transports, which would be permitted to exceed Mach 1 over land.
The dream of supersonic commercial flight shelved since the retirement of Concorde in 2003, could become reality again.
Contact the author: thomas@thedrive.com