The Pentagon’s top watchdog has released a report that offers new details and insights into the U.S. Navy’s struggle to resolve long-standing issues with the Engine Air Particle Separators, or EAPSs, on U.S. Marine Corps and U.S. Air Force V-22 Osprey tilt-rotors. This includes the revelation that there was never any requirement for the EAPS design to meet specifications from Rolls-Royce, the manufacturer of the aircraft’s two engines, to ensure proper operation in all desert conditions.
EAPS failures, and by extension instances of catastrophic engine power loss and other serious issues, have been factors in a number of fatal Osprey crashes in the past decade. The Navy is on its third attempt to redesign the separators, and now the entire engine inlet configuration, in as many years. There are concerns that it may still not be able to ensure that its latest effort will adequately reduce the risks of V-22s sucking up dangerous amounts of particulate matter, especially when operating in desert environments.
The Department of Defense’s Inspector General published the final report of its review of Navy EAPS redesign efforts on Nov. 7, 2019, but only released a redacted copy publicly on Nov. 12. The service initiated the latest project to improve the particle separators on the Ospreys last year. It had made two attempts to solve the issues in 2010 and 2011, but “determined that neither redesign was a viable option,” according to the watchdog’s report. The Navy is the lead service for the V-22 program overall and the Osprey Joint Program Office is part of Naval Air Systems Command (NAVAIR).
“The third EAPS redesign is intended to remove more soil from the air flowing into the V‑22 engine than the original EAPS; however, the soil ingested into the engine would be four times greater than the engine manufacturer’s specification allows,” the report explains in its executive summary. “As a result, the V‑22 remains at risk despite more than nine years of EAPS redesign attempts.”
Both Marine MV-22s and Air Force CV-22s – which reached initial operational capability in 2007 and 2009, respectively – have a pair of Rolls-Royce T406 engines, also known as the AE 1107C-Liberty, which drive their two huge propellers. Each engine has an EAPS, which, in principle, is supposed to use a vacuum force to pull soil and other particulate matter out of the airstream before it gets inside. There is no indication that the engine/EAPS configuration is different on Japan’s V-22s or on the Navy’s own forthcoming CMV-22 variant.

Ospreys produce an absolutely massive amount of rotor wash during short and vertical takeoffs and landings with their engines tilted upward. The blast is so strong that when Marines rushed to Nepal in the aftermath of the devastating earthquake there in 2015, their MV-22s had to avoid certain landing zones for fear of knocking over already weakened structures nearby.
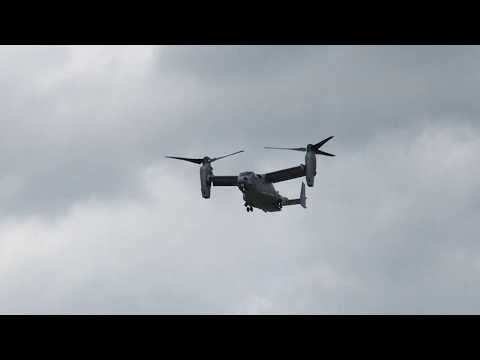
It can also throw up an immense amount of soil, sand, and dust, often enveloping the aircraft, creating what is called a Reduced Visibility Landing situation, or RVL. That material can reduce the amount of air getting to the engine, which can lead to a loss of power. If it gets sucked up inside, it can adhere to fan blades, case walls, and more, potentially leading to more serious issues. Sands with high alkali metal concentrations are particularly dangerous as they can melt in the heat of the engine and actually fuse to sensitive parts.

EAPS problems, especially when combined with operations in sandy environments, have been linked to a number of serious and sometimes fatal accidents. This includes a notable MV-22 crash in Hawaii in May 2015 that killed two Marines and injured 20 more. The official accident investigation blamed pilot error, though it also recommended developing a new air filter and changing regulations to further reduce the maximum amount of time Ospreys could remain hovering inside a dust cloud from 60 to 35 seconds.
The new Inspector General report underscores that problems with the EAPS, and subsequent impacts on the engines, have been well known since at least 2010, when the first attempt was made to redesign the system. At that time, the Navy expected the engines on the Ospreys to each run for about 500 flight hours before personnel on the ground would need to swap them out. The service had found that, in reality, this could be as low as 200 hours for V-22s flying regularly in desert conditions.

At that time, the U.S. military had already been involved in conflicts in Iraq and Afghanistan, where sand and dust are common environmental factors, for nearly a decade. The United States remains engaged in those countries, as well as in Syria, a significant part of which is also desert.
In addition, between 2008 and 2015, there were also at least eight “engine rapid power loss events” directly attributed to particulate ingestion in the engine. “Although the eight engine rapid power loss events did not result in a catastrophic accident, the engines had degraded to a point where engine failure was possible,” the report notes.
It is unclear how many “particulate-induced engine rapid power loss mishaps” V-22s have experienced since 2007, but the Navy says that there have not been any reported since it began implementing other risk mitigation techniques “more than four years ago.” This has included establishing additional limitations on total allowable flight time in sand and dust clouds, improved low engine power warning systems, and updated training regimens. We also don’t know how many other mishaps that did not involve a catastrophic power loss can still be directly attributed to particulate buildup in the engine. Officially, the Osprey has a very good safety record, despite long-standing perceptions to the contrary.


What we do know is that the Navy was aware of the limitations of the EAPS from the very beginning.
“When the PMA‑275 [the V-22 Joint Program Office] developed the specification for the original EAPS design, it did not require the EAPS to meet the Rolls‑Royce specification in all desert environments,” the report notes. Beyond that, “PMA‑275 did not include a … specification for the EAPS to define the amount of soil the EAPS would remove from the air, and subsequently the concentration of soil that would remain in the air and be ingested into the V‑22 engine.”
So, in 2010, the Navy hired the Bell-Boeing team behind the V-22 to develop an interim improved EAPS with better performance. The next year, with that first effort still ongoing, the service handed them another contract to craft a more lasting solution that would meet Rolls-Royce’s specifications.
“Initial flight testing of the first EAPS redesign resulted in inconsistent results,” according to the Pentagon’s Inspector General. “For example, one test showed an improvement in the amount of time that the engines could operate in desert environments, while another test showed a decrease.”
The second effort was beset by delay and difficulties and the Navy finally canceled it altogether in December 2017. The following year, the service again hired Bell and Boeing to initiate a third redesign program, which is still ongoing.

The Pentagon’s Inspector General is also warning that the Navy may not know whether the third EAPS redesign truly works in the end, either, because the service is not planning to test it against all types of representative material that Opsreys might encounter. None of the soil samples in the test plan, at present, include all three of the major components found around the world.
“The composition of the soils that exist worldwide include three main components: sand, silt, and clay,” the report explains. “For example, one soil composition the PMA‑275 intends to use to test the third EAPS redesign is 0.0‑percent sand, 100.0‑percent silt, and 0.0‑percent clay and another is 100.0‑percent sand, 0.0‑percent silt, and 0.0‑percent clay.”
The Navy challenged that assertion, saying that the particulate matter it will use in forthcoming tests of the new separator system will produce the same kind of impacts as real-world soil compositions. The service has also challenged the Inspector General’s core finding that it did not develop an EAPS that meets Rolls-Royce’s specifications, but has, in doing so, highlighted a larger issue. The argument is that it cannot be faulted for not doing this because, given the limitations that Osprey’s present design impose, it is simply not technically possible to do so without a significant rework of major components.
The main problems revolve around the engine inlet design and the reality that the Osprey has significantly different engine airflow requirements and parameters when operating in as a traditional aircraft from when it is hovering like a helicopter. The second EAPS redesign program specifically found that installing air filters that would be able to provide adequate protection while in hover mode prevented the engine from getting enough air in airplane mode.
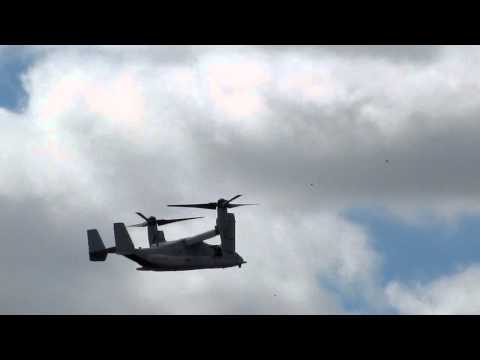
The Navy, in cooperation with U.S. Special Operations Command and the Air Force, is presently in the midst of completely redesigning the engine inlets on the Ospreys as part of its third EAPS redesign effort. The Improved Inlet Solution (IIS) dates back to at least 2014, based on heavily redacted documents the author previously obtained via the Freedom of Information Act, something not mentioned in the Inspector General’s report. The scope of the IIS work has already led to “cascading effects” on cost as new issues have emerged, including the need for additional anti-icing features around a new auxiliary nacelle door that allows for additional airflow while the V-22 cruises like an airplane.


The Navy also says, rightly, that it is unreasonable to assume that any aircraft will be able to operate without issue for protracted periods of time in sandy, dusty, and similar environments and that its holistic approach to mitigating the risks was not taken into account. The service has also said in the past that these issues are of limited concern, in general, because pilots typically spend 10 seconds or less in these risky conditions.
At the same time, the service has repeatedly downplayed these issues despite knowing their very real impacts and has often blamed serious mishaps on pilot error first and foremost. “A proper risk assessment should have prompted the pilots to choose an alternate flight profile, path or landing site that would have minimized or avoided the severe brownout conditions,” the Marine Corps said in a statement after the release of the investigation into the 2015 Hawaii crash.
When and if Marine and Air Force V-22s receive the new IIS kit remains to be seen. The Navy says that it expects to complete an initial evaluation of the new system using static engine test rigs next year. The “data will inform updates to the IIS system specification prior to preliminary design review,” the service added in its response to the Inspector General’s findings and recommendations.
In the meantime, those services will continue flying Ospreys that have EAPS installed that the Navy knows have limited effectiveness and not only do not, but cannot conform to Rolls-Royce’s specifications.
Contact the author: joe@thedrive.com